For multi-factory/workshop planning, PlanMateAPS provides different solutions based on the company’s production scale, BOM structure, and production process characteristics.
Co-scheduling of assembly and parts is a difficult part of production planning, which usually includes plans for multiple branches or independent workshops, and is responsible for different production management. Usually the assembly plan corresponds to customer demand, and parts production needs to supply the assembly plan. Usually BOM is divided into multiple levels, many of which have virtual levels. In addition to the virtual level, each level has a separate work order.
- The number of work orders at all levels does not match. When ERP starts work orders, in order to simplify production management, component work orders often merge multiple requirements. In addition, the processing time also affects the size of the work order. The number of work orders with long processing time is smaller, and the number of work orders with short processing time is larger. After long-term order changes, defective scrapping and other factors, it is difficult to establish a correlation between work orders at all levels.
Large-scale ERP will match work orders at all levels based on the BOM structure. The basic algorithm is as follows:
- Finished product work orders determine demand times based on the order’s delivery date, and then calculate start and finish dates. If a work order matches multiple orders, the date is set based on the earliest demand.
- The half-product work order matches the superior work order. If a half-product work order matches multiple superior work orders, the start date will be calculated based on the earliest demand date.
It can be seen from the above algorithm that the production time of parts is based on the earliest date of subsequent work orders, which results in the premature production time of many half-finished work orders.
- Each branch has independent plans and is not closely related. For example, if a mold in an injection molding factory fails and a part cannot be produced, the reasonable approach is to immediately notify the electronics production and assembly factory that the product should not be scheduled for production, but it is very difficult to implement. Since there is no one-to-one correspondence between work orders and parts are shared by multiple products, it is difficult to determine which orders are affected.
The first step in scheduling is to divide the boundaries and determine the scope of the planner’s work. The principle of division is that the boundaries are clear and the complexity of the plan is controllable.
The first issue that needs to be clarified is how many people are responsible for scheduling, that is, how to draw boundaries. We do not recommend creating a very complex plan. If there are too many devices and complicated process relationships, the spider web-like connections on the Gantt chart will make it difficult to see the logic clearly, making it extremely difficult to analyze and modify the plan.
Although APS schedules automatically, the production plan should be under the control of the planner. Abnormal production schedules, order changes, equipment failures, etc. all require manual intervention to modify the plan. Therefore, the number of equipment that each production management is responsible for tracking should be within the controllable range. within.
Example of separation scheme by production process:
- Finished product assembly
- PCBA
- Injection molding
- Sheet metal processing
Problem: Unbalanced workload of each student management department
Separated by workshop area:
For example, a machine processing factory has 4 large workshops, each with about 200 pieces of equipment, and the responsibilities are divided according to the workshop. According to this allocation method, each process of a product cannot span across workshops.
Problem: A product may be produced in different workshops, and the load of each workshop is unbalanced in each time period. This can be solved through capacity analysis and order allocation between workshops.
PlanMateAPS adopts different solutions for enterprises of different sizes.
Unified scheduling: For small-scale enterprises, although the production is divided into workshops + BOM layering, if the total number of equipment is not large and the complexity is not high, one person can usually be responsible for scheduling. The system’s plan is to match hierarchical work orders and establish the contextual relationship between work orders, and APS schedules them based on the matching results.
BOM structure
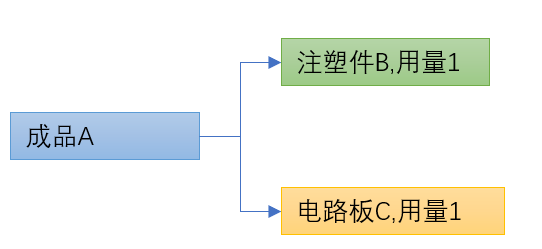
Work order list
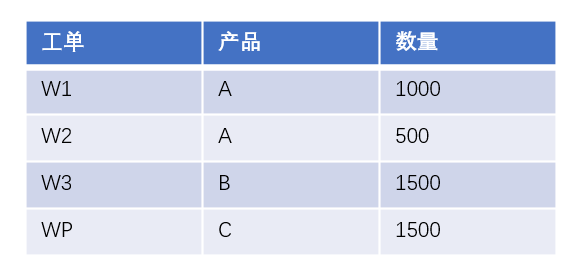
process schedule
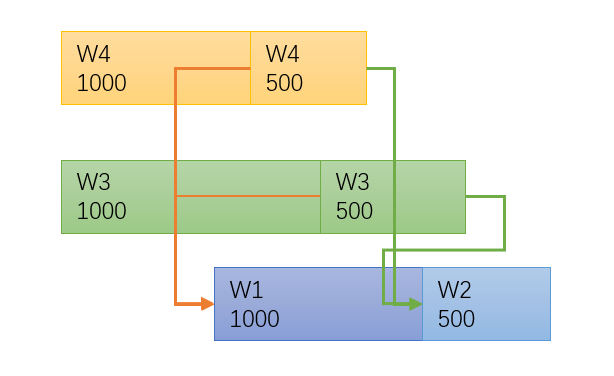
If it is a large enterprise, the work order matching method in Solution 1 above will cause the relationship to be too complex, the logic unclear, and beyond the controllable range of the planner.
For large enterprises, after boundary demarcation, multiple planners schedule independently. APS establishes mutual constraints between multiple plans based on the BOM structure.
- The output plan of parts is converted to in-transit inventory, and assembly uses in-stock + in-transit inventory constraint scheduling.
- The process before this method requires a certain locking time. It is assumed that during the locking period, the half-product production plan has been determined and it is inconvenient to modify. During the locking time, material constraint scheduling is used. After locking the time, schedule production according to the demand date
Grading plan diagram
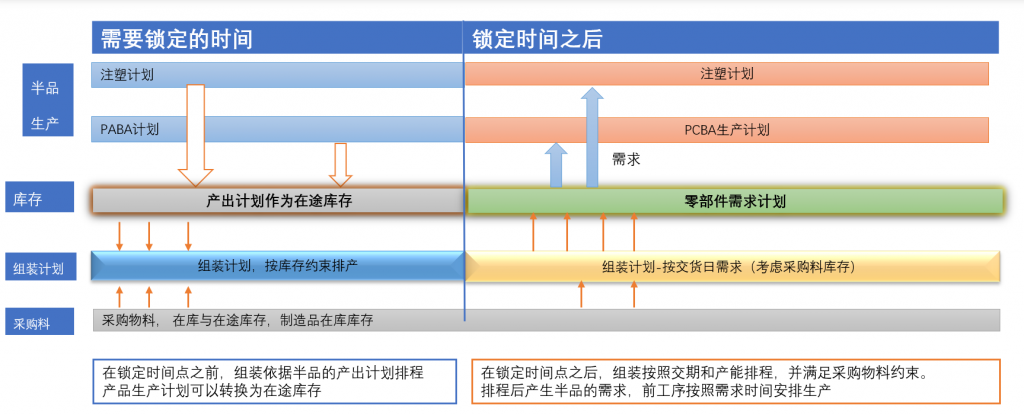
Multi-process collaborative workflow
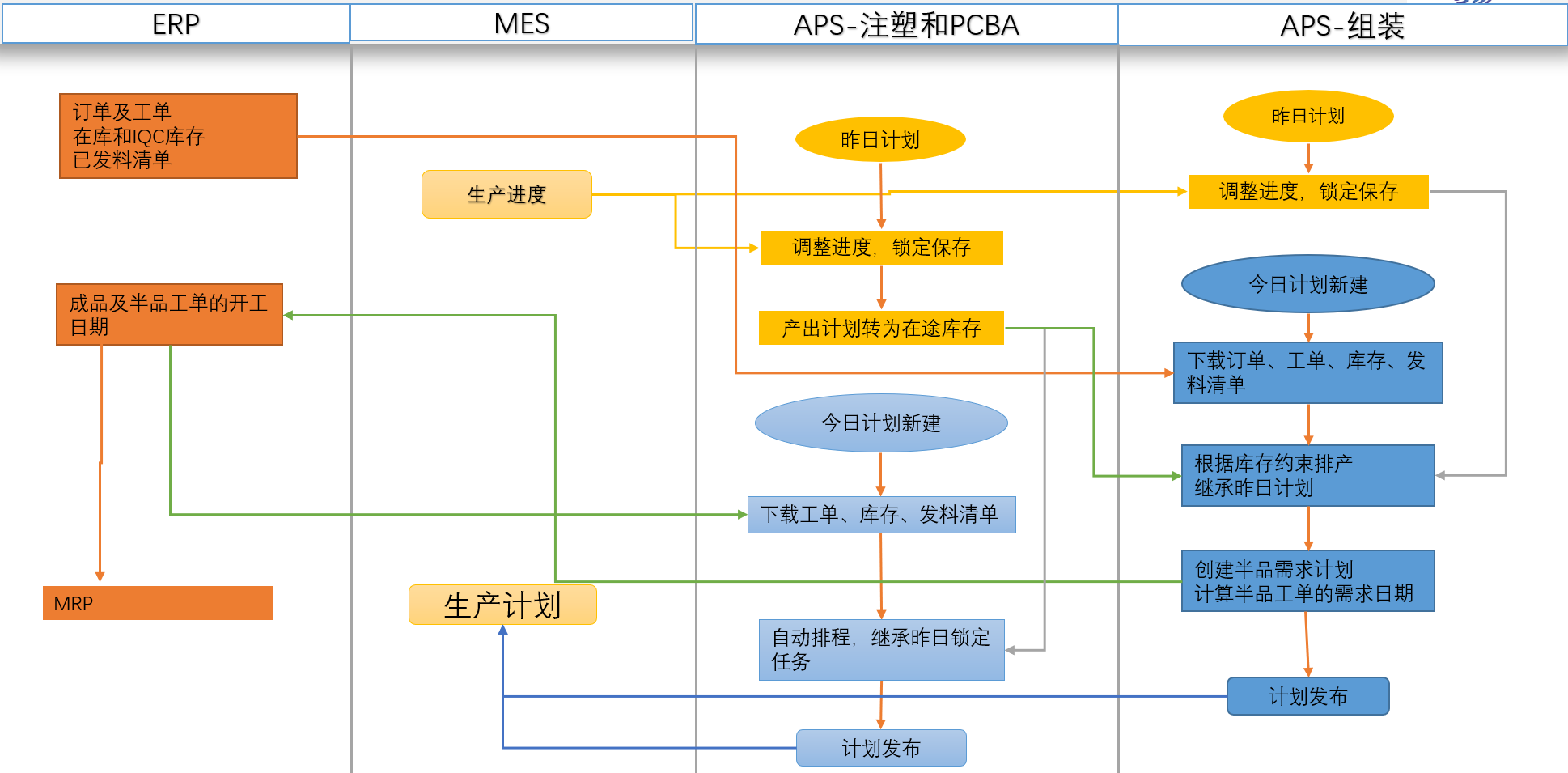
相关资讯
了解更多APS知识