The core of APS is the detailed production plan, which is also the plan that the workshop actually executes every day.
For companies that have introduced ERP systems, detailed production plans are based on work order scheduling. If the product BOM is divided into multiple levels, usually ERP will start work orders at different levels, and APS will schedule work orders at all levels.
Key points of the plan include:
- Matching relationships must be established between multi-level work orders. Due to differences in production capacity and technology, the number of work orders at all levels usually cannot be matched one by one, and a matching relationship must be established before running the schedule.
- The plan satisfies all necessary constraints, including process model constraints and material constraints.
- Optimization goals include on-time delivery, equipment utilization, reducing switching, shortening WIP time, etc. It is necessary to comprehensively consider various optimization goals and not just consider a single goal.
- Plan inheritance and continuity
- Connection and consistency with actual production progress
- Quick modification and rearrangement
The detailed production plan of PlanMateAPS is accurate to the second. After the calculation is completed, we get:
- Detailed production planning for all master resources.
- Usage plan for auxiliary resources (molds, fixtures, etc.).
- manpower demand planning
- Work order material requirements and shortage list
- Purchasing referral program
The production plan is displayed in a Gantt chart, which provides a visual representation of the production plan. The interactive Gantt chart has rich plan editing and modification functions, allowing users to track progress and quickly modify plans.
Primary Resource Gantt Chart
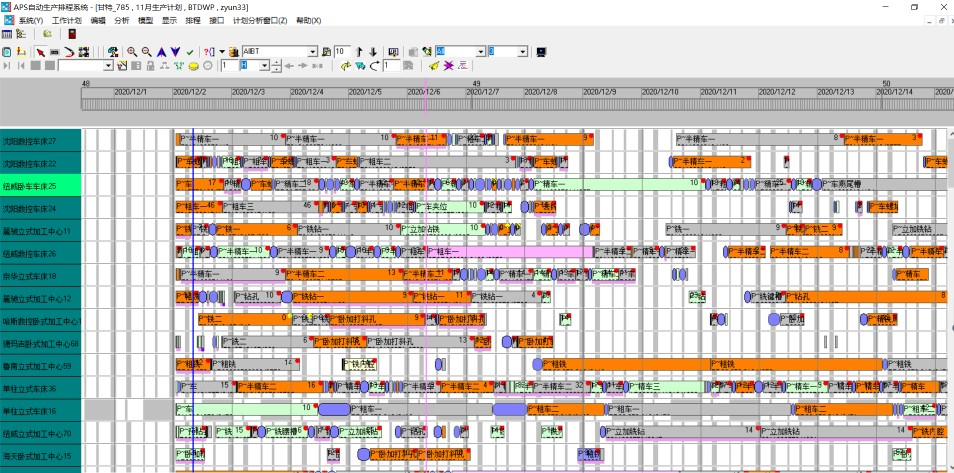
Work order process
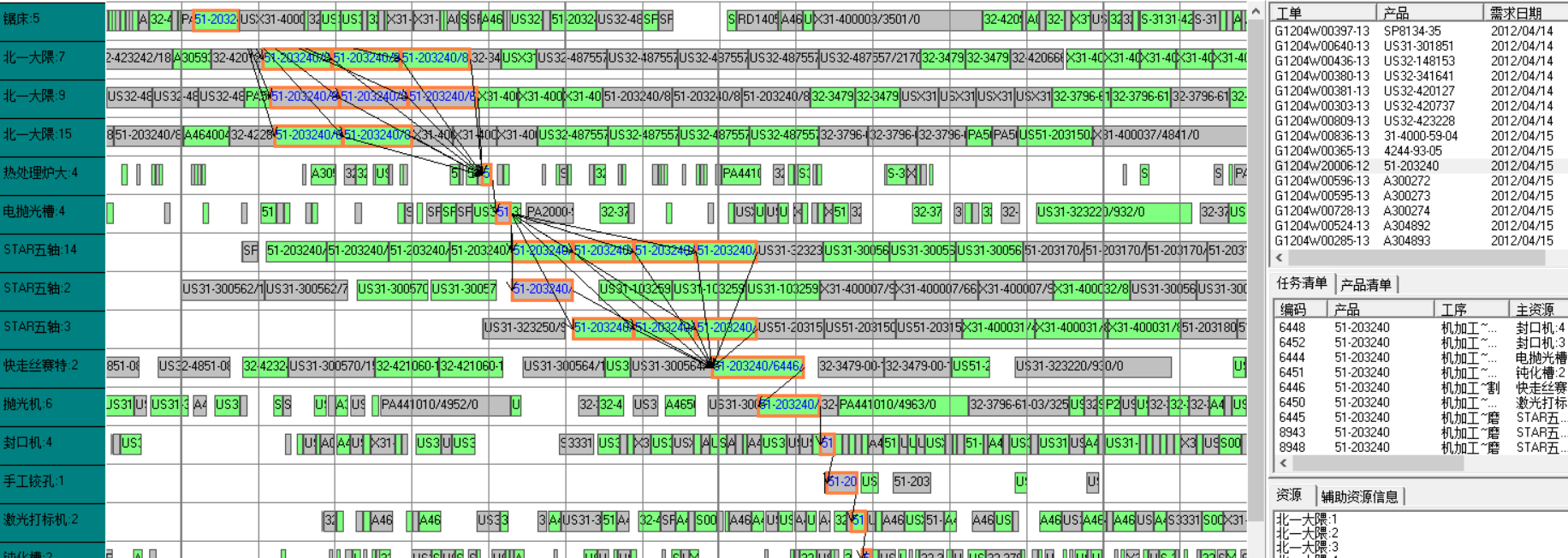